Expert Tips for Reducing Downtime with Efficient Fleet Repair Practices
Discover expert strategies for minimizing downtime with efficient fleet repair practices. Keep your heavy-duty trucks on the road with tips from Fleetgo.
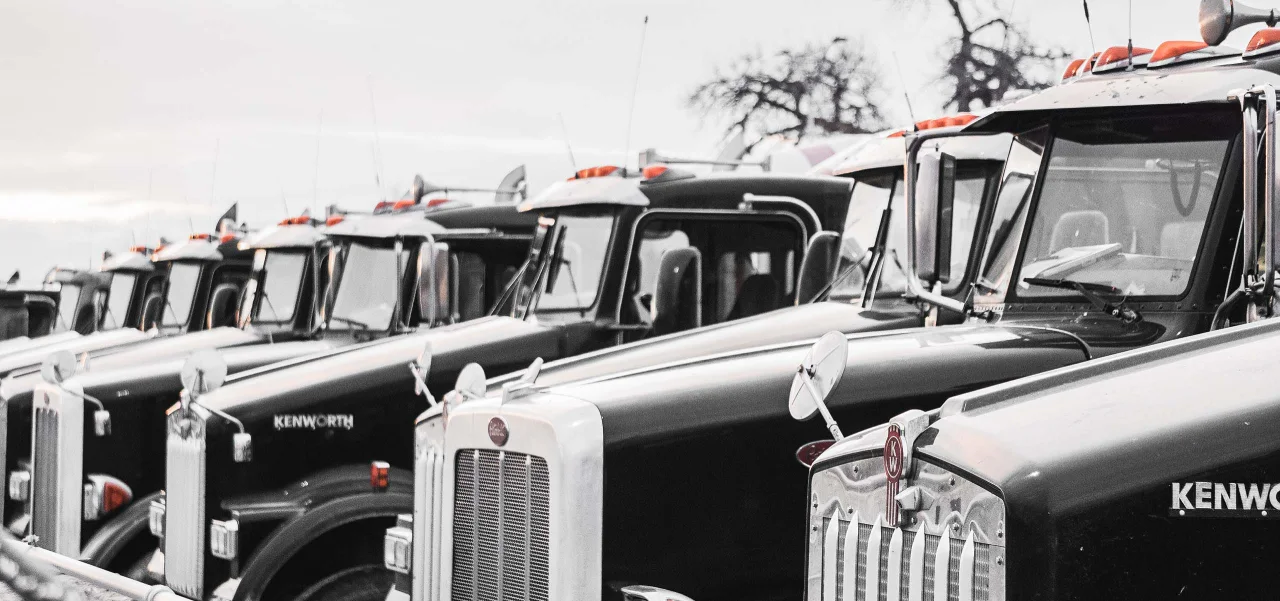
Every minute a heavy-duty truck is off the road translates into lost revenue and missed opportunities. So how can you keep your trucks rolling and your business growing? Well, with the right fleet repair practices, you can significantly reduce downtime and keep your fleet running smoothly. At Fleetgo Heavy Duty Inc., we focus on proactive solutions that prevent lengthy repairs and costly halts in your operations. Here are some expert tips to help you maintain efficiency and ensure that your trucks spend more time on the road than in the shop.
1. Implement a Preventive Maintenance Program
A preventive maintenance program is crucial for minimizing unexpected truck breakdowns. It’s best to address issues before they escalate into larger problems. Here are some essentials to think about when creating a preventive maintenance program:
- Regular Inspections: Schedule regular inspections for key components such as brakes, tires, engine systems, and suspension. Catching wear and tear early can prevent costly failures down the line.
- Scheduled Fluid Changes: Keep up with regular oil, coolant, and transmission fluid changes. This not only extends the life of your truck's components but also ensures optimal performance.
- Use Diagnostic Tools: Invest in advanced diagnostic tools that can monitor and predict when parts are likely to fail. This allows for proactive repairs instead of reactive fixes.
2. Train Your Drivers
Your drivers are your first line of defense against unplanned downtime. Properly trained drivers can spot issues before they escalate and can even perform basic maintenance tasks. Drivers should conduct routine checks on tire pressures, fluid levels, and lights daily to catch issues before they escalate. Encourage safe driving and efficient communication with the maintenance team can prevent many potential problems. Best practices for your drivers include:
- Routine Checks: Train drivers to perform daily checks on their vehicles, including tire pressure, fluid levels, and lights. These small checks can prevent bigger issues from developing.
- Safe Driving Practices: Encourage safe and efficient driving practices. Aggressive driving can lead to premature wear on your vehicles, increasing the frequency of repairs.
- Communication: Ensure drivers know how to communicate potential issues to the maintenance team quickly. Early reporting can mean the difference between a quick fix and a lengthy repair.
3. Optimize Repair Workflow
An optimized repair workflow is crucial for minimizing downtime when repairs are necessary. The repairs times may depend on damage and your repair shop’s expertise but your own preparation may reduce downtime. For efficient repairs that reduce your workload, keep the following in mind:
- Maintenance Records: Keep detailed, centralized records of all maintenance and repairs for each truck. This helps in diagnosing issues faster and ensures no routine maintenance is overlooked.
- Parts Inventory Management: Maintain a well-organized inventory of essential parts. Waiting for parts to be ordered can significantly extend downtime, so having the necessary components on hand speeds up the repair process.
- Prioritize Repairs: Not all repairs are created equal. Prioritize repairs based on their impact on vehicle performance and safety. For example, brake issues should be addressed immediately, while minor cosmetic repairs can be scheduled for later.
4. Use Quality Parts and Skilled Technicians
The quality of parts and the expertise of your technicians play a significant role in how quickly and effectively repairs can be completed.
- OEM Parts: Whenever possible, use Original Equipment Manufacturer (OEM) parts for repairs. They are specifically designed for your trucks and are more reliable than aftermarket alternatives.
- Skilled Technicians: Employ skilled and experienced technicians who understand the intricacies of heavy-duty trucks. Their expertise will not only lead to faster repairs but also fewer mistakes that could cause future downtime.
- Ongoing Training: Ensure that your technicians receive ongoing training to stay updated on the latest technologies and repair techniques. This continuous learning will improve repair efficiency and effectiveness.
5. Embrace Technology
Leverage technology to streamline your fleet maintenance and repair processes.
- Fleet Management Software: Implement a comprehensive fleet management software that tracks maintenance schedules, repair histories, and parts inventory. This software can alert you when maintenance is due, helping you stay ahead of potential issues.
- Telematics Systems: Use telematics systems to monitor vehicle health in real-time. These systems can provide data on engine performance, fuel efficiency, and other critical metrics, allowing you to address issues before they lead to a breakdown.
- Mobile Repair Units: Consider using mobile repair units that can perform repairs on-site. This minimizes the time trucks spend in the shop and gets them back on the road faster.
6. Analyze and Improve
Continuous improvement is key to reducing downtime over the long term.
- Downtime Analysis: Regularly analyze downtime data to identify patterns or recurring issues. This analysis can help you pinpoint areas where processes can be improved or where more frequent maintenance might be necessary.
- Benchmarking: Compare your downtime rates with industry benchmarks to see how your fleet stacks up. This can provide valuable insights into areas where you might need to improve.
Conclusion
Reducing downtime is all about being proactive, organized, and efficient. By implementing a robust preventive maintenance program, training your drivers, optimizing your repair workflow, using quality parts, embracing technology, and continuously analyzing and improving your processes, you can keep your fleet on the road where it belongs. With these expert tips, Fleetgo Heavy Duty Inc. can help ensure that your trucks spend more time hauling loads and less time sitting idle. If you’re curious about how to choose the right fleet repair shop, check out our fleet tips before making your decision.
Contact FleetGo
Get in touch with Fleetgo today to request a quote or to schedule in-shop or mobile services in Edmonton & the surrounding area! Our mobile service extends to a 100km radius around Edmonton for emergency roadside assistance & mobile truck & fleet repairs, including Sherwood Park, Spruce Grove, Fort Saskatchewan, St. Albert, Stony Plain, along Highway 16, & more!
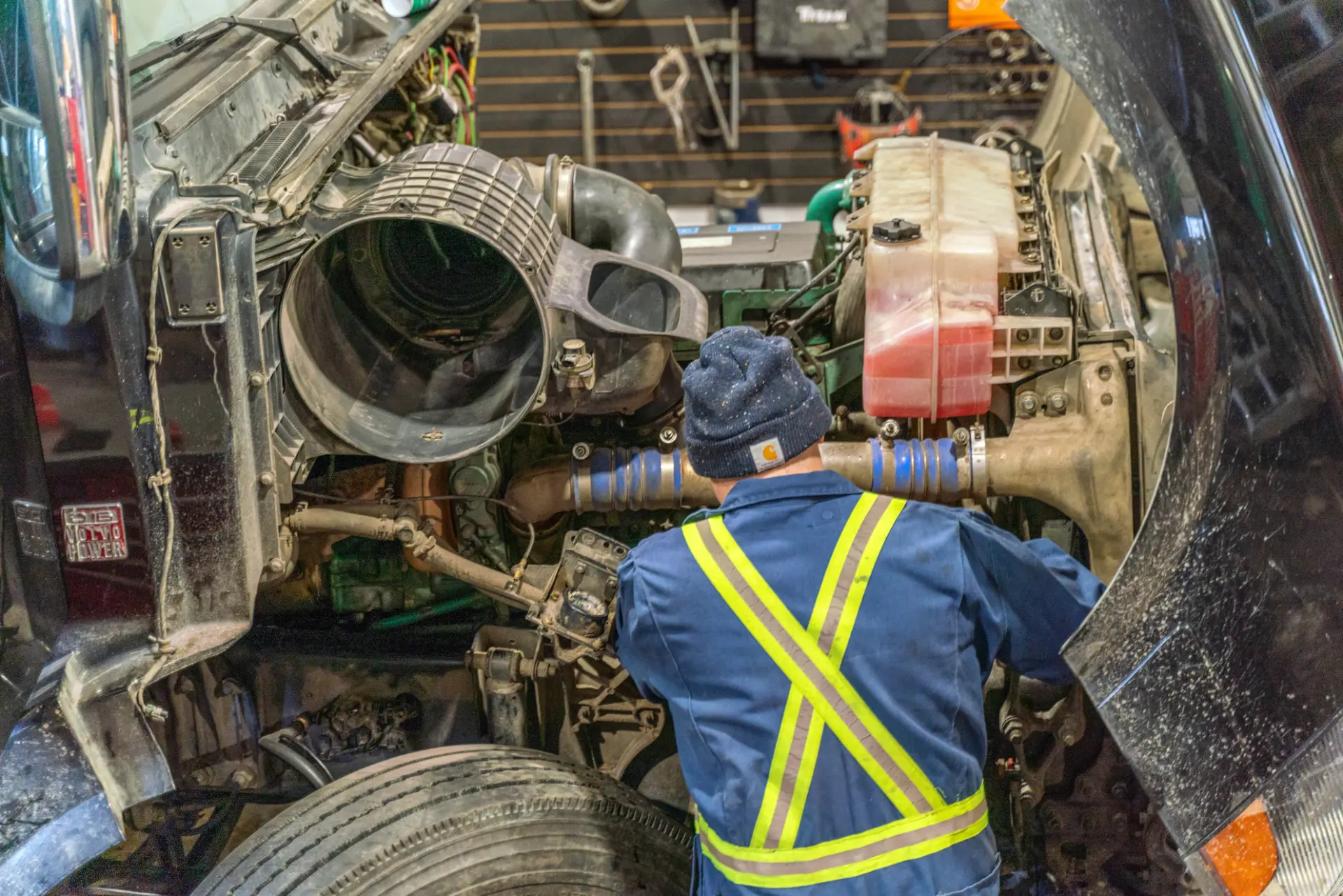